Comprendre : Les 5 phases de l’APQP
APQP est une méthode pour la standardisation du système de management de la qualité généralement utilisée dans l’industrie automobile et aéronautique, mais quelles sont ces avantages ?
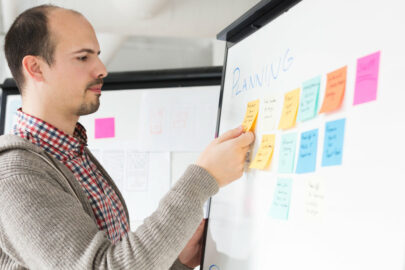
APQP est une méthode pour la standardisation du système de management de la qualité généralement utilisée dans l’industrie automobile et aéronautique, mais quelles sont ces avantages ?
L’APQP, pour Advanced Product Quality Planning, est une démarche préventive d’obtention de la qualité sur des développements de nouveaux produits. Mais également une méthode pour la standardisation du système de management de la qualité généralement utilisée dans l’industrie automobile et aéronautique.
Il est crucial de souligner le rôle critique du fournisseur dans la garantie de la qualité et de la conformité des produits ainsi que dans l’efficacité du processus de développement.
L’APQP a tout d’abord été développée dans l’industrie et le secteur automobile, en interne, dans le cadre de la norme QS9000, par les trois constructeurs Chrysler, General Motors et Ford. En Europe, le système est également reconnu pour son efficacité dans la gestion des processus de développement et de fabrication, y compris les projets de développement de produits et les projets de révision, d’amélioration.
L’APQP est un élément stratégique dans la gestion de la qualité, influençant non seulement la maîtrise des processus de développement mais aussi la satisfaction client.
Ainsi, l’Advanced Product Quality Planning est une méthodologie d’amélioration continue par laquelle les entreprises peuvent réduire considérablement les coûts et les délais, et améliorer la qualité des produits par anticipation (méthodes préventives). Elle est utilisée dans deux cas : APQP est également une méthodologie de gestion de projet qui intègre des étapes, livrables et jalons nécessaires au développement de produits et à l’industrialisation.
La méthode peut être utilisée à différents stades dans le cadre d’un projet de développement et de fabrication d’un nouveau produit. Elle participe aux étapes d’analyse, de conception des produits tout au long de leur développement, de la validation des processus et des nouveaux produits finis.
Elle peut aussi être utilisée pour améliorer les processus de fabrication dans une entreprise. Au cours de l’analyse et de la conception, les processus de fabrication peuvent être améliorés par le transfert des meilleures pratiques d’une partie du processus à une autre ou à un autre processus qui touche d’autres produits.
L’APQP (Advanced Product Quality Planning) est une méthode de planification de la qualité avancée largement utilisée dans l’industrie aéronautique et automobile. Cette méthode vise à garantir la qualité des produits tout en réduisant les coûts de production. L’APQP repose sur une approche structurée qui implique la participation de tous les acteurs du processus de développement de produits. Les principaux objectifs de l’APQP sont de :
• Cette méthode est très efficace, car elle implique la participation de tous les acteurs concernés, dont la direction, les opérateurs de chaque processus, les ingénieurs et les techniciens.
• La méthode a également pour avantage d’impliquer les partenaires commerciaux et le client final pour une meilleure compréhension de leurs besoins.
• Les délais et les coûts sont réduits grâce à cette méthode.
• Le transfert des meilleures pratiques d’un processus à un autre dans le même produit ou entre différents produits permet aussi de réduire les coûts.
• Elle est par ailleurs très flexible, car elle permet aux entreprises de modifier leurs processus en fonction des modifications intervenant dans leur secteur d’activité.
Ainsi, cette méthode est très intéressante pour les entreprises qui ont beaucoup d’activités et qui veulent améliorer la qualité de leurs produits.
• La mise en œuvre de l’Advanced Product Quality Planning.
• L’amélioration continue de l’APQP.
• La gestion des risques.
• Le suivi, le partage et l’amélioration des résultats.
L’APQP (Advanced Product Quality Planning) est intrinsèquement lié à la notion de qualité. Cette méthodologie vise à garantir que les exigences qualité sont prises en compte dès les premières étapes du développement d’un produit. En intégrant la qualité au cœur de la démarche APQP, les entreprises peuvent anticiper et prévenir les problèmes potentiels avant qu’ils ne surviennent en production. Selon une étude menée par l’Observatoire de la Qualité en 2023, les entreprises françaises ayant adopté l’APQP ont constaté une amélioration moyenne de 40% de leur taux de conformité dès la première production.
Cette approche proactive permet non seulement de réduire les coûts liés à la non-qualité, mais aussi d’augmenter la satisfaction client. Par exemple, Renault a réussi à diminuer de 25% ses retours clients sur les nouveaux modèles lancés après la mise en place de l’APQP.
Le processus APQP est une démarche structurée qui guide les équipes à travers les différentes étapes du développement et de la production d’un produit. Ce processus se décompose en cinq phases distinctes, chacune avec ses propres objectifs et livrables. L’un des aspects clés de l’APQP process est son caractère itératif et collaboratif. Il encourage la communication entre les différents départements de l’entreprise, favorisant ainsi une approche transversale de la qualité. Une enquête menée par l’IATF (International Automotive Task Force) en 2022 a révélé que 78% des entreprises ayant mis en œuvre l’APQP process ont constaté une amélioration significative de leur time-to-market.
Par exemple, l’équipementier automobile Valeo a réussi à réduire de 30% le temps de développement de ses nouveaux produits grâce à l’application rigoureuse du processus APQP. Cette approche structurée permet non seulement d’optimiser les ressources, mais aussi d’assurer une meilleure maîtrise des risques tout au long du cycle de vie du produit.
L’outil qualité DFMEA (Design Failure Modes and Effects Analysis) permet de s’assurer que les fonctions et les performances décrites dans le cahier des charges sont prises en compte.
L’outil qualité PFMEA (Process Failure Mode Effects Analysis) permet, à travers une analyse minutieuse des composants, systèmes et sous-systèmes, de s’assurer que les dysfonctionnements et les problèmes identifiés sont pris en compte.
L’outil qualité PPAP (Production Part Approval Process) permet d’approuver et de valider le produit, ses composants, ses pièces (qu’elles soient nouvelles ou révisées). Il faut que le processus soit compris, le produit également, et qu’il soit possible de démontrer comment passer de l’un à l’autre.
L’outil qualité SPC (Statistical Process control), quant à lui, permet de vérifier le processus en cours et permet de faire des vérifications ponctuelles afin de diminuer au maximum les taux d’erreurs ou de corrections par effet d’anticipation.
Enfin, l’outil qualité MSA (Measurement System Analysis) permet de comprendre les flux qui existent dans le processus et comment sont-ils mis en place afin de déduire à la fois la qualité et l’applicabilité dudit processus.
Cette dernière étape permet de lancer la phase de production, de contrôler et de maintenir un suivi strict de cette dernière, mais aussi d’évaluer continuellement la performance du produit et du processus qui le sous-tend.
👉 Découvrez notre formation Les Core Tools de l’APQP et développez une expertise qui transformera vos projets en succès. En savoir plus
Ça peut vous intéresser
Tous les articlesLe Lean Management, initialement développé pour le secteur manufacturier, est désormais largement adopté dans divers secteurs, y compris celui des services. En se concentrant sur l’élimination des gaspillages et l’amélioration continue, le Lean Management offre des opportunités significatives pour optimiser les opérations, améliorer la qualité du service et accroître la satisfaction des clients. Cet article […]
Le Lean Management est une méthodologie centrée sur l’élimination des gaspillages et l’optimisation des processus pour maximiser la valeur pour le client. Depuis son origine dans l’industrie automobile japonaise, le Lean a été adopté par des entreprises du monde entier, dans divers secteurs, avec des résultats impressionnants. Cet article analyse plusieurs cas réels d’entreprises ayant […]
SMED ou Single Minute Exchange of Dies en anglais, pour changement rapide d'outillage, est une méthode qui vise à diminuer le temps de changement d'outils de production et de réglage entre deux séries.
Demande de devis
Un projet de formation ? Demandez votre devis
Service gratuit
Téléchargement du catalogue
Yellow Belt Lean 6 Sigma
À partir du 23 octobre 2025
Green Belt Lean 6 Sigma
À partir du 19 septembre 2025